Viktor Laier ist Business Developer bei Industrial Analytics IA in Berlin und einer der Speaker beim 25. VDI-Kongress AUTOMATION.
Prescriptive Maintenance wird mit KI- und Automatisierungstechnologien zum Game-Changer
Ungeplante Stillstände, damit verbundene Kosten sowie Produktionsausfälle verhindern, gleichzeitig die Sicherheit und Zuverlässigkeit im Anlagenbetrieb steigern: Die Vorteile einer vorausschauenden Wartung – Predictive Maintenance – sprechen für sich. Neue Konzepte gehen nochmals darüber hinaus: Prescriptive Maintenance zielt darauf ab, mittels Technologien wie Künstlicher Intelligenz und Machine Learning die Betriebsbedingungen noch exakter zu steuern und die Instandhaltung von Anlagen noch zielgerichteter zu planen. Wird die vorausschauende Wartung damit zu einem echten Game-Changer? Mit dieser Fragestellung wird sich Viktor Laier, Business Developer, Industrial Analytics IA GmbH, Berlin, im Rahmen des 25. VDI-Kongresses AUTOMATION befassen.
„Im Kern verfolgen wir dabei den Anspruch, die Kompetenz von Ingenieuren und Data Scientists zu vereinen, um so zu noch exakteren Prognosen zu gelangen. Dadurch werden Maschinenbetreiber in die Lage versetzt, Wartungszyklen zu optimieren, Kosten für Ersatzteile zu reduzieren und die Lebenserwartung der Maschine zu verlängern“, gibt Laier eine erste Vorschau auf seinen Vortrag. Neben der Optimierung der Wartungsprozesse verbindet er mit Prescriptive Maintenance aber noch zwei weitere wesentliche Vorteile: „Auf Basis der Datenanalysen lassen sich Optimierungspotenziale identifizieren, sodass die Maschinenbetreiber konkrete Handlungsempfehlungen für optimierte Einstellungen erhalten, um die Effizienz und Produktivität ihrer Anlagen zu steigern. Die dritte Säule betrifft das Energie Management: Durch eine kontinuierliche Performance-Überwachung wird es möglich, datenbasierte Maßnahmen zu treffen, um Energieverbräuche zu reduzieren und Effizienzen zu verbessern – wichtig mit Blick auf die Anforderungen an ESG-Reportings und die Nachhaltigkeitsziele der Unternehmen.“
Case Study aus der Energieversorgung
Im Rahmen des Automatisierungskongresses macht Laier die Potenziale anhand eines konkreten Fallbeispiels deutlich. Im Beispielprojekt geht es um ein Energieversorgungsunternehmen, das künstliche Intelligenz und Automatisierungstechnologien nutzt, um die Effizienz in Bezug auf Zuverlässigkeit und Kosten zu steigern. Allerdings: Ein rein statistisches Modell reicht nicht aus, um eine komplexe Maschine wie einen Kompressor vorherzusagen, betont Viktor Laier: „Daher sind physikbasierte Modelle erforderlich, sogenannte First-Principle-Modelle. Ein zentraler Aspekt beim Aufbau effektiver prädiktiver Analysen durch maschinelles Lernen ist daher die Etablierung physikbasierter digitaler Zwillinge.“
Vorteile von First-Principle-Modellen
First-Principle-Modelle sind für die Überwachung und Optimierung großer rotierender Maschinen effizienter als rein statistische Modelle, weil sie auf den physikalischen Gesetzen und mechanischen Zusammenhängen der Maschinen basieren, so der Referenz weiter: „Die Modelle berücksichtigen die spezifischen Eigenschaften und das Verhalten der Ausrüstung, wie zum Beispiel die Kräfte und Belastungen, denen sie ausgesetzt ist, die Materialien, aus denen sie hergestellt sind, und die Art und Weise, wie sie verwendet werden.“
Vor diesem Hintergrund und angesichts der herausfordernden Marktsituation im Energieversorgungsbereich hat ein norddeutsches Unternehmen damit begonnen, First-Principle-Modelle auf seine Kompressordaten anzuwenden. Prescriptive Maintenance dient in diesem konkreten Fall dazu, um die Betriebszeit der Maschinen und die Versorgungssicherheit für die Kunden zu gewährleisten. Ein weiteres wichtiges Ziel stellt die Verlängerung der Wartungszyklen durch vorausschauende Wartungsstrategien dar.
Vibrationsdaten als wertvolle Basis
Die Installation von Vibrationssensoren bildete im Projekt zunächst den ersten Schritt, um wertvolle Informationen über den Zustand und die Leistung von Maschinen zu sammeln. Der Vorteil dabei Maschinenvibrationen reagieren hochsensibel auf Veränderungen in der Maschine und können somit frühzeitig über Veränderungen des Maschinenzustandes informieren und warnen. Nachdem die Dateninfrastruktur und Konnektivität eingerichtet waren, begann Industrial Analytics mit der Anwendung von Algorithmen für maschinelles Lernen auf historische und Echtzeitdaten der Kompressoren des Versorgungsunternehmens. Viktor Laier erklärt: „Nach drei Monaten intensiver Arbeit waren die First-Principle-Modelle und digitalen Zwillinge betriebsbereit, was zu mehr Erkenntnissen und einem Mehrwert führte.“
Nachhaltige Optimierungen erzielt
Die bereits erzielten Ergebnisse sprechen dabei für sich: Mit dem kompletten Predictive-Maintenance-Service konnten bereits in den ersten sechs Monaten wichtige Meilensteine erreicht werden. Wartungszyklen konnten aufgrund des verbesserten Wissens über den Kompressor und eines KI-basierten Vorhersagesystems, das die Wartungsingenieure bei der Planung unterstützt, verlängert werden. Dadurch könnten bei geringerem Ersatzteilverbrauch Ressourcen bis zu 30 Prozent eingespart werden. Vor allem aber konnte der Energieversorger die unerwarteten Ausfallzeiten der Kompressoren enorm reduzieren und errechnete eine Steigerung der Betriebszeit um 70 Prozent.
Wie dieser Anwendungsfall zeigt, dürfte der Einsatz von KI- und Automatisierungstechnologien zur Überwachung und Optimierung in der Gastransport- und Speicherindustrie für Anlagenbetreiber, Versorgungs- und Energieunternehmen ein wichtiger Baustein der Zukunft sein, um die Effizienz zu verbessern und die Versorgungssicherheit zu gewährleisten. Hinzu kommen die hohen Anforderungen, die ohnehin an Einrichtungen der Kritischen Infrastruktur gestellt werden. Doch darüber hinaus ergeben sich aus Sicht von Viktor Laier noch viele weitere Anwendungsfelder für Prescriptive Maintenance: beispielsweise bei Kläranlagen, Großanlagen in der Fertigungsindustrie, der Kraftwerkstechnik und Turbomaschinen – bis hin aber auch zur Gebäudeautomation.
Hybridmodelle für eine optimierte Anlagensteuerung
Das Grundprinzip ist dabei stets dasselbe: Industrial Analytics verwendet hybride Modelle zur Überwachung des industriellen Prozesses und der Maschinen. Diese Hybridmodelle verwenden First-Principle- oder Physik-basierte Modelle zusammen mit maschinellem Lernen. Die Modelle können thermodynamische Prozessmodelle der Anlage sein, die mit historischen Daten ausgestattet sind. Sie werden verwendet, um dynamische Simulationen des Anlagenverhaltens durchzuführen oder Erwartungswerte zu berechnen. Dabei sind die Modelle für die industrielle Prozesssimulation so konzipiert, dass sie auf der Grundlage historischer Daten mit einem Minimum an Informationen flexibel angepasst werden können.
Zur Person
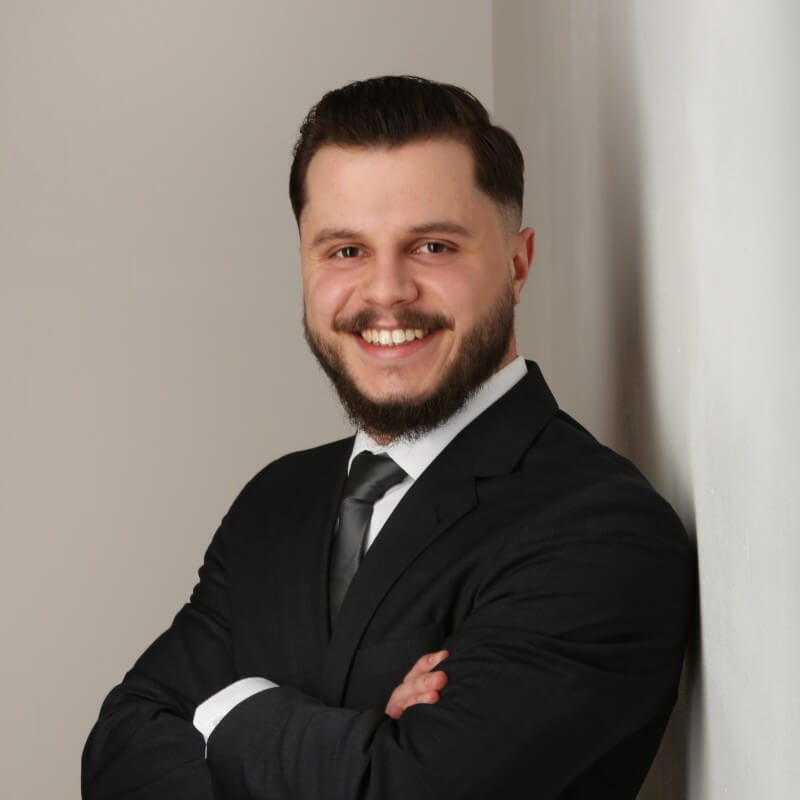
Quelle: Industrial Analytics